3D Printed Fixtures

Facts
Category
Problem owner
Wind OEMs
Project period
Total budget
1,011,300 kr.About the project
Fixtures for the Production of Components for the Wind Turbine Industry
Fixtures for producing components for the wind turbine industry are typically manufactured manually, a process that is often time-consuming and costly. This project develops and implements methods for 3D printing fixtures, reducing fixture costs by 80%.
Challenge
Manual manufacturing of fixtures for components in the wind turbine industry is often time-consuming and costly. 3D-printed fixtures can reduce downtime from 2–3 weeks to just 24 hours in production.
Proposed Solution
3D-printed fixtures can reduce time-to-market, minimize downtime in production lines, and achieve cost savings of 80% for subcontractor companies in the wind turbine industry.
Project Deliverables
Methods and guidelines for 3D printing fixtures.
Project in the media
Videos
Want to learn more?
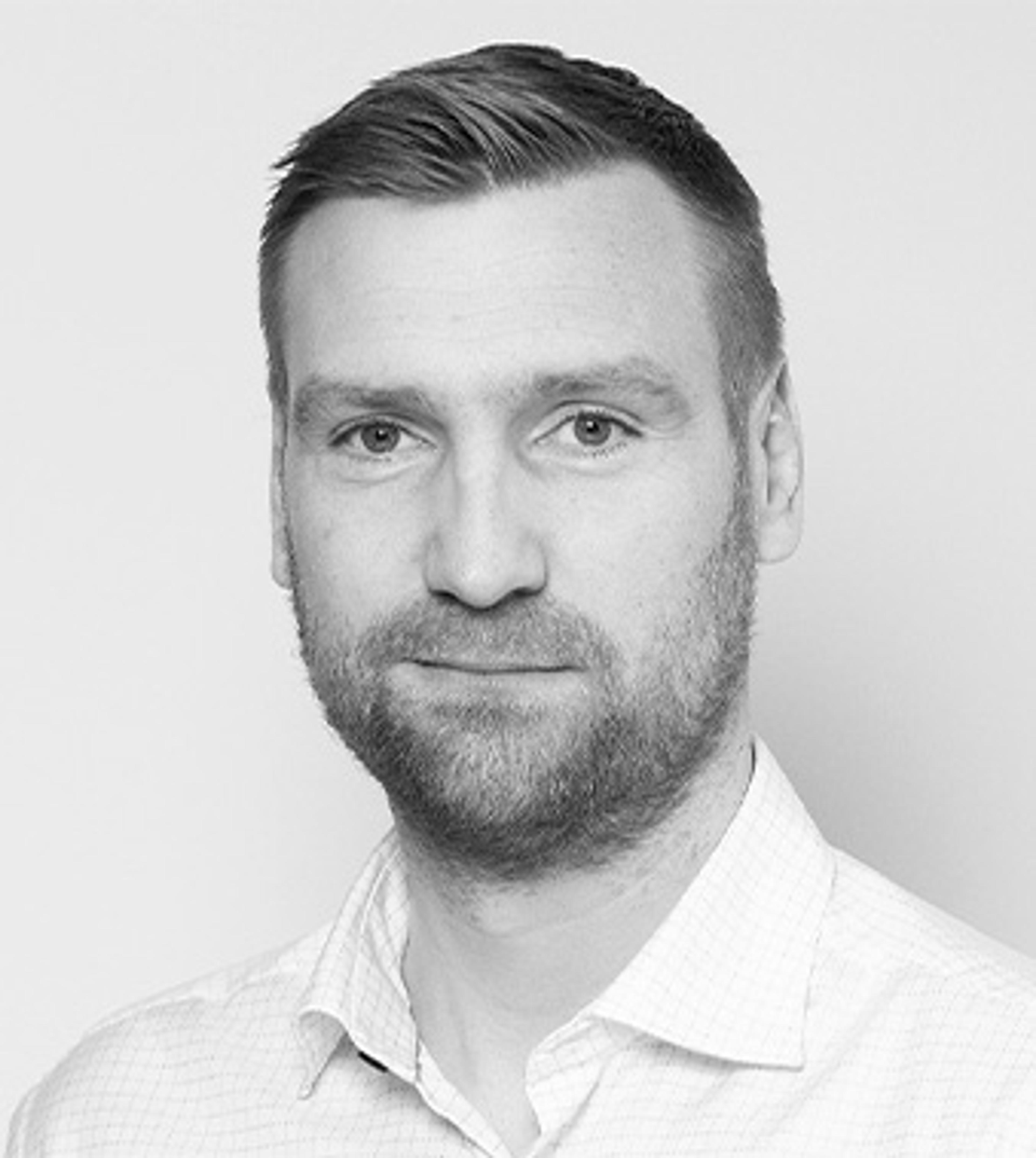
Skibsbyggerivej 5, 3. sal.
9000 Aalborg
Navitas
Inge Lehmanns Gade 10
8000 Aarhus C
House of Offshore Innovation
Kanalen 1
6700 Esbjerg
Port House
Vendersgade 74
7000 Fredericia
BLOXHub
Bloxhub, Bryghusgade 8, 3. sal,
1474 København K
Energy Cluster Denmark
Nørre Havnegade 43
6400 Sønderborg
©Energy Cluster Denmark 2025